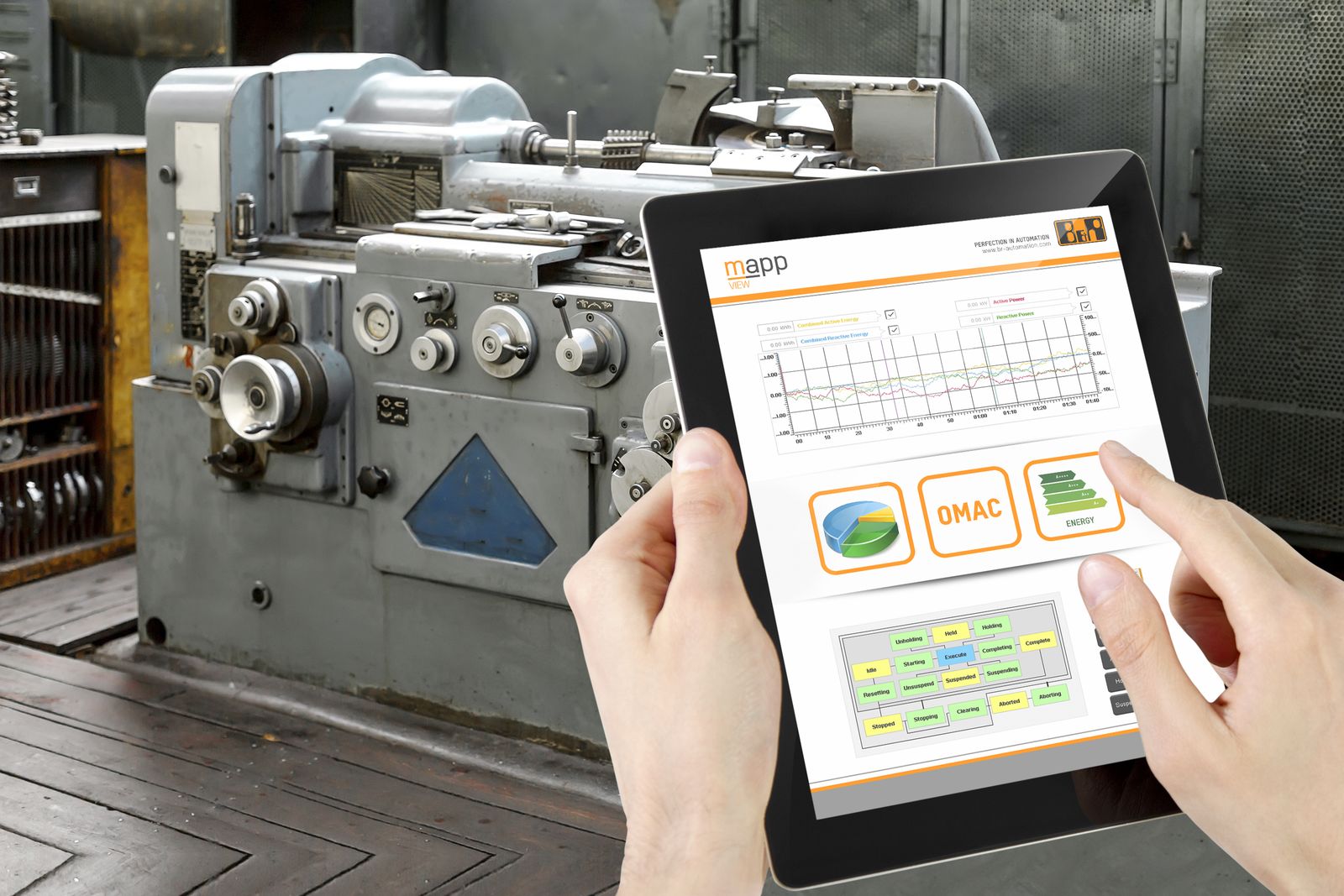
La importancia del diagnóstico preventivo y correctivo con el uso de herramienta en software
En la actualidad el área de mantenimiento es la más importante en la cuestión del buen desempeño de la maquinaria y, por ende, que nuestra producción cumpla con la demanda requerida, aquí se torna vital el diagnóstico preventivo y correctivo para reducir costos y aumentar la productividad.
Toda la maquinaria ha evolucionado a donde ya es vital un proceso automatizado por medio de un controlador lógico. Un cerebro en el proceso y quién determina paso a paso, cómo se comportan nuestro conjunto de equipos.
Todo lo anterior no sería funcional sin un conjunto de dispositivos como motores, sensores, señales digitales y analógicas, fuente de alimentación, etc. Todos nuestros equipos tienen un tiempo de vida útil, por lo que los fallos en nuestra máquina se irán presentando conforme los años pasen. Y, por ello es importante, además de un diagnóstico preventivo, ajuste y limpieza, un diagnóstico correctivo en el momento del daño.
Si nuestro personal no se encuentra preparado para los posibles daños en la máquina, el tiempo se puede convertir en el peor enemigo por las pérdidas a partir de este paro repentino.
El uso de las herramientas correctas puede ayudar a tener una respuesta de primera mano y actuar de forma adecuada ante el daño, implementando un diagnóstico preventivo y correctivo. Nuestro controlador lógico, además de realizar todo el proceso, también recibe retroalimentación de sus componentes donde podemos determinar qué está presentando problemas.
El proceso para poder determinar la falla, será variante según el caso, en algunas ocasiones el sistema de diagnóstico ha sido agregado por el programador directo en la HMI. En otras ocasiones, es necesario conectarnos al PLC para así poder visualizar la información.
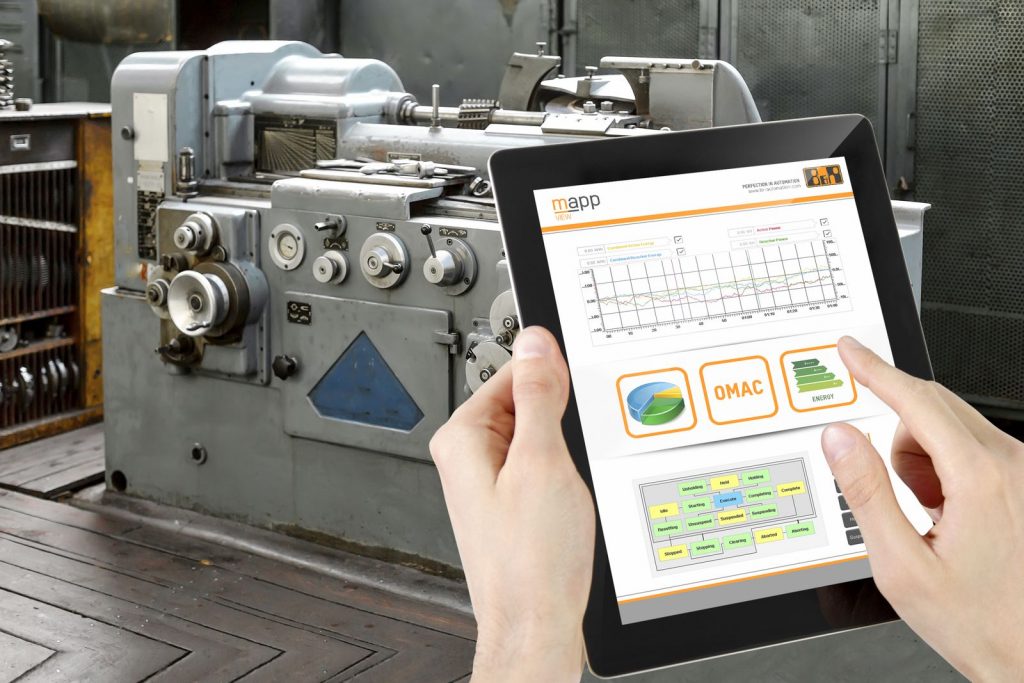
¿Para qué sirve?
A grandes rasgos, el uso de herramientas adecuadas, son muy útiles para poder encontrar el fallo en el menor tiempo posible y poder repararlo en un tiempo aceptable.
Aunado al diagnóstico, es necesario tener un buen plan de refaccionamiento, esto es identificar qué proveedor cumple con un buen stock y, si no existe algún proveedor con algún equipo de la máquina, tener esta pieza en un almacén propio. Además de realizar un análisis de equipos de riesgo y lo problemático tener en stock para una respuesta rápida.
En conexión con nuestro PLC podemos visualizar nuestro hardware y si alguno presenta problemas podemos observarlos, y así tener una guía certera de dónde comenzar con nuestra reparación.
En la actualidad, la pantalla muestra información del fallo, pero no exactamente de qué se trata, sin conexión al PLC no tenemos toda la información. Así que en ese momento se inicia con la reparación a forma de prueba y error, lo que puede llegar a resolver el problema, pero podría llevar mucho tiempo y esfuerzo. En muchas de las ocasiones no se logra dar con el verdadero problema utilizando este método poco factible.
¿Qué beneficios trae?
- Reducción en paros de máquina con un buen diagnóstico preventivo.
- En caso de paro de máquina, un tiempo corto en encontrar el error.
- Revisión en vivo con la máquina, visualizando el hardware de nuestra máquina y valores.
- Se pueden forzar señales para determinar si nuestro sensor o actuador funciona correctamente.
- Análisis a nuestros ejes para visualizar el correcto funcionamiento.
- Histórico de errores desde que se instaló el PLC, así poder ver fallas que hayan sucedido anteriormente y si se ha repetido.
Partes básicas del diagnóstico preventivo y correctivo
Para lograr un diagnóstico preventivo y correctivo adecuadamente es necesario estar online con nuestro PLC, para lo cual es necesario algunas partes básicas:
- Que el PLC permita la conexión online con el usuario, por default esta opción está activa, pero el programador puede desactivar esta opción.
- El PLC debe contar con puerto Ethernet, pues por este medio se realiza la conexión. En versiones anteriores también se puede realizar por serial, pero no es tan funcional como lo actual.
- Contar con la IP del PLC, en caso de no tenerlo, se puede buscar en conexión por Ethernet, pero no siempre se encuentra la IP.
- En caso de un servicio remoto por parte de un técnico, contar con team viewer o algún otro programa que permita el control a la computadora que está conectada al PLC.
- Si es posible, contar con el programa fuente de la máquina.
Todo lo anterior mencionado es respecto a mi experiencia en el diagnóstico preventivo y correctivo con la marca en control B&R, pero esto puede variar respecto a las diferentes marcas que existen en el mercado.
Santiago Alonzo
Lo sentimos, los comentarios están cerrados en este momento.